Through new design automation technology developed at the University of Guelph, engineering researchers have created a cost-effective way to produce customized face masks that are more comfortable and offer better protection against airborne particles.
In the wake of the COVID-19 pandemic, face masks have become an indispensable part of daily life. But the effectiveness of a mask is entirely dependent on how well it fits the face of the person wearing it. One-size-fits-all masks can leave gaps, compromising comfort and protection.
Dr. Sheng Yang, professor in the College of Engineering and Physical Sciences, and his team began to consider the prospect of a face mask with a customized fit.
“We wanted to develop technology that can facilitate the rapid development of custom-fit masks or respirators through automation,” Yang explains. Exploratory research revealed customized face masks did in fact exist, but they were costly and took a long time to procure.
Algorithms advance comfort, protection
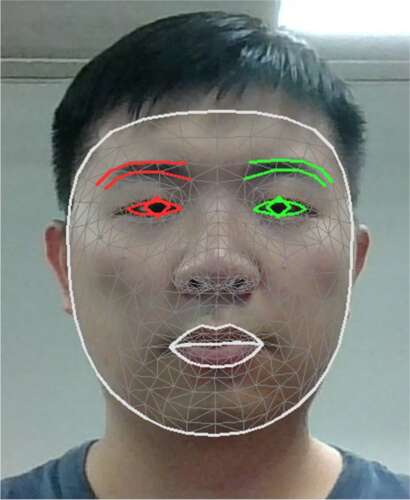
The team’s video-based approach requires a person to take a five-second recording of themselves, capturing their facial features. The video, equipped to capture angles and facial expressions, is then cropped into frames (still images) to focus in on points of interest like one’s face, nose, mouth or the distance between their eyes. These references enable as realistic a digital design as possible.
This detailed data is then uploaded to design software and advanced algorithms generate a custom mask model tailored to one’s specific facial shape, improving a mask’s overall effectiveness.
Automating the process eliminates the need for a designer, saving time and money. “It’s low cost, compared to traditional manufacturing methods like casting,” Yang says. “Here we use automation and 3D printing to achieve a custom fit.”
Participants who tried on the 3D-printed masks reported a comfortable fit that allowed them to move their jaw and make facial expressions without discomfort.
One challenge Yang notes is the limited 3D printable medical-grade materials available. The protection a mask provides comes from both the material it is made from and the filters inside. The face mask is a supporting structure in contact with one’s face, he describes, while the filter is mounted on top of that. The manufacturing of filters is commercialized and beyond the scope of the design phase.
Technology applicable beyond PPE, health care settings
There are also advantages the technology provides beyond personal protective equipment.
“This kind of knowledge can be reserved for future uses,” Yang says. He has already been contacted by a doctor who treats patients with sleep apnea, interested in how this technology could be applied to customized respirators, or continuous positive airway pressure (CPAP) machines.
Yang also envisions the technology being used to produce sportswear or any customized product that fits human features, such as hands, feet or even teeth, designing helmets, gloves, goggles, shoes or dental implants.
“We believe this technology can significantly improve public health and safety,” says Yang.
This study is published in The International Journal of Advanced Manufacturing Technology and funded by a discovery grant from the National Sciences and Engineering Research Council of Canada.
Contact:
Dr. Sheng Yang
syang19@uoguelph.ca