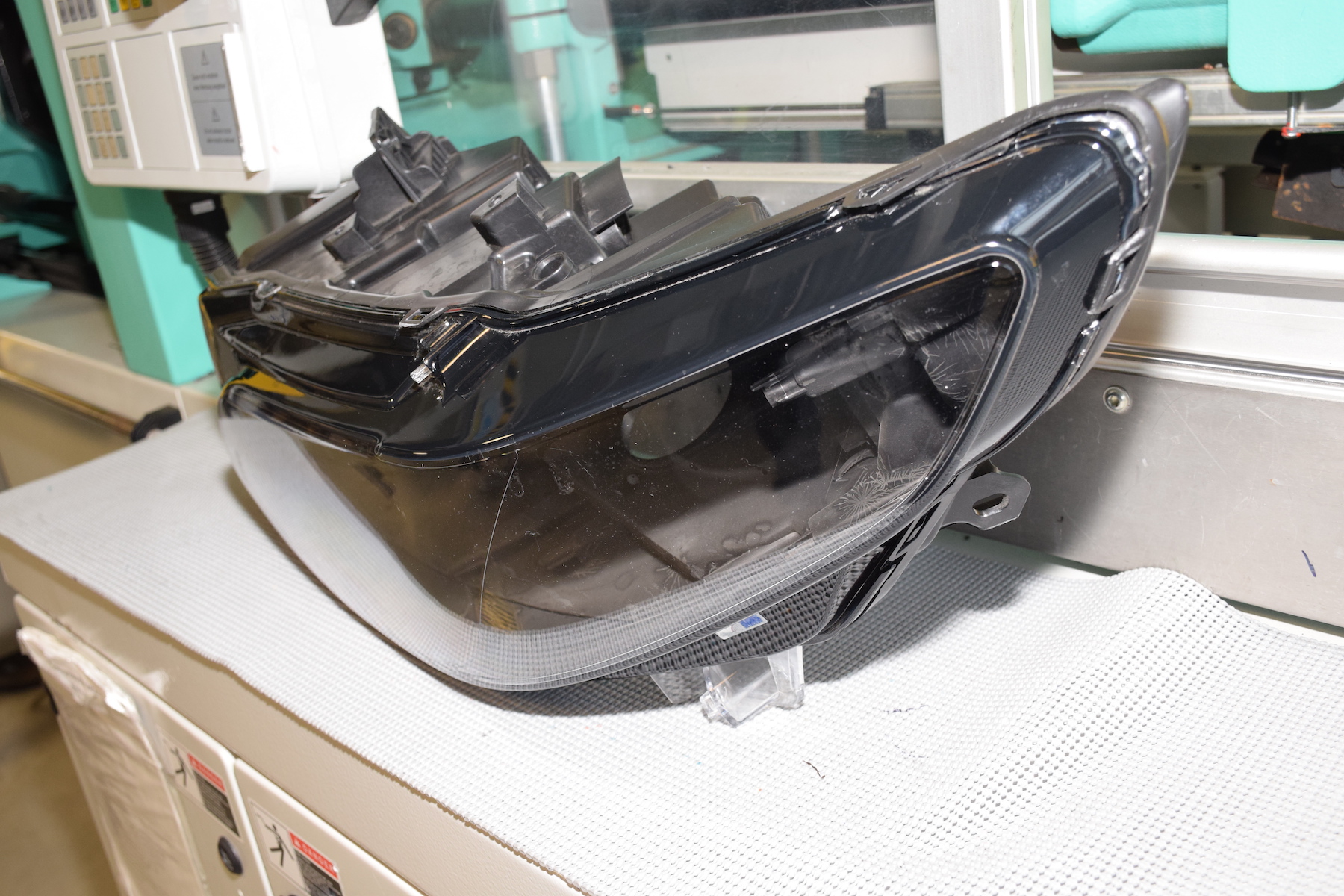
You could call it “coffee to go.”
Made from coffee bean waste from McDonald’s Corp., bio-composite materials developed and tested at the University of Guelph will be used for the first time to create vehicle parts made by Ford Motor Co.
Following initial development and two years’ worth of process and product testing by researchers in U of G’s Bioproducts Discovery and Development Centre (BDDC) and at Ford, the automaker will use waste coffee bean skins from McDonald’s roasting facilities to make lighter and more sustainable headlight housings for its Lincoln Continental.
“This technology is an excellent example of implementing innovative ideas developed here at the University of Guelph to find green alternatives to petroleum-based products, benefiting the environment, the economy and consumers,” said Prof. Amar Mohanty, director of the U of G centre.
Currently, about 1.2 million pounds of coffee bean skins, called coffee chaff, are thrown away, strewn in fields or burned every week in North America. The material will now be used as a bio-based alternative for plastic car parts made by Ford.
Atul Bali, CEO of Competitive Green Technologies (CGT) based in Leamington, Ont., and a technology licence partner with the University, said the parts are nearly 20 per cent lighter, meaning greater fuel efficiency for drivers, and could yield significant energy savings during production.
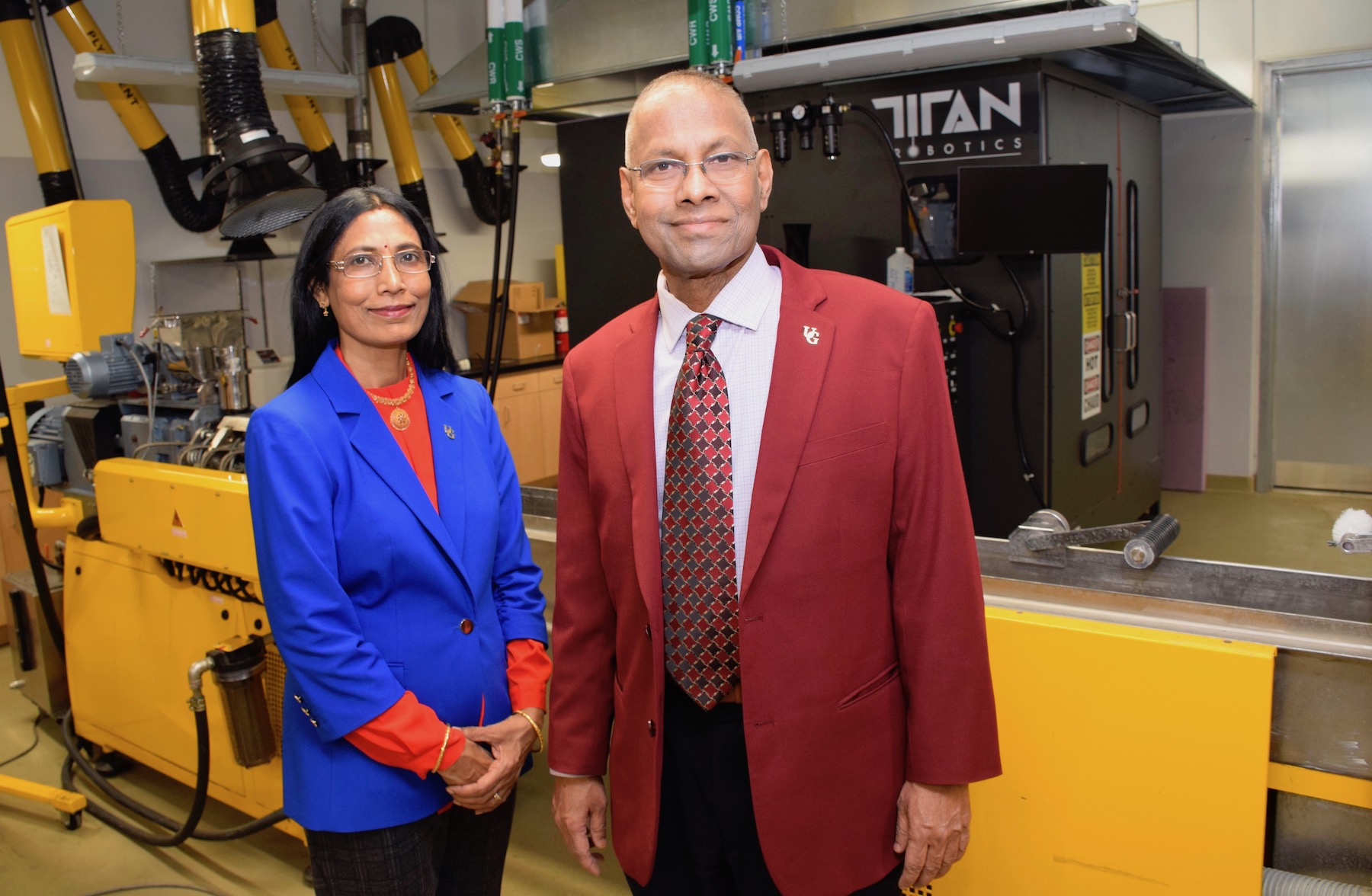
The technology was developed and patented by BDDC researchers, who study ways to make bio-composite alternatives to petroleum-based products, including car parts and other consumer goods.
The BDDC works with Competitive Green Technologies, which makes bio-composite resin using coffee waste from McDonald’s. The resin is used to mould headlight housings manufactured by Varroc Lighting Systems, near Ford’s Dearborn, Michigan, headquarters.
“We are the exclusive licencees for the University of Guelph to make this formulation,” said Bali. Working with U of G, the company began testing resins two years ago. After numerous trials, he said, “three months ago, we managed to meet all the performance requirements. It was a labour of love and determination.”
Prof. Manjusri Misra, who is cross-appointed between the School of Engineering and the Department of Plant Agriculture, said, “It has been a true collaborative effort to bring this innovation to fruition.”
Added Mohanty, who also holds a cross-appointment between plant agriculture and engineering, said, “Now the BDDC will be involved in refining bio-composites for other planned vehicle parts.”
In 2015, the BDDC team and CGT developed the world’s first fully compostable coffee pod along with Toronto-based coffee roaster Club Coffee.